LMS – Real time line monitoring system
Results achieved so far, innovation’s expected benefit for society
The product provides continuous feedback on the status of the production lines. This could help to reduce downtime and save costs throughout the production process. The product has already been certified in one factory, where it is in continuous daily use (0–24). Furthermore, two new manufacturing partners are planning to introduce the product.
References, awards, media releases
COLLABORATING PARTNERS
Manufacturing: Sanmina, ITNH Kft. NPI Flux (in Serbia), Dyntell Magyarország Kft. Incubator: START IT @ K&H (social media release), Start It UP Győr
Professional platform: Mesterséges Intelligencia Koalíció (Artificial Intelligence Coalition), EKKV (based on a cooperation, we have developed a curriculum on the presentation of SMT for the e-learning platform of EEKV), Széchenyi István University’s Alumni Magazine – interview with Smart4Factory
Steps necessary for further development
The enterprise is currently in the process of leaving the startup status and entering the Hungarian and the international markets. Therefore, in order to grow, we would need an ever-growing network of contacts to be able to attract new partners. The product is aimed to be used mainly by the SME sector and since it is an “out-of-the-box”, ready-made product, we provide a simple, fast, and cost-effective solution for enterprises.
Short description of the innovation
The LMS (Line Monitoring System) can be useful for any manufacturer of printed circuit boards (SMT – Surface-Mount Technology factory) because it provides real-time feedback from the production line. This could help reduce cases of slowdown of production or downtime, which eventually results in saving costs. Due to the Plug&Play design of the Bi-Box that is part of the system, integration can be carried out even during production.
The company was founded in 2019 by Tamás Szaif, who came up with the idea to develop a system that provided a unique solution, unrivalled on the market at that time. In cooperation with Benjámin Horváth, a company was founded to develop a system for monitoring production (a so-called Line Monitoring System) especially designed for manufacturers of SMT (Surface Mounted Technology) printed circuit boards. Soon, László Szabó also joined the company as the third owner, and he is also the person responsible for the company’s marketing and entry to the market. To this day, the company is owned exclusively by Hungarian owners. The LMS provides instant feedback for the operator working at the production line about the disturbances and stoppages during production. Another advantage of the system is that engineers and maintenance personnel, as well as the management of the SMT factory using the line monitoring system can access additional information on the activities conducted as well as about downtime periods recorded in the factory. Data can be displayed on the screen of a computer, a tablet or even on a mobile phone.
It is safe for us to say that this solution provides the possibility for the manager of the company to fit all data of the production into his/her pocket, since he/she can access accurate and instant information on the current status of the production anywhere, anytime at the tip of his/her fingers. Information provided by the system can be used to implement measures to minimize losses that have not been identified earlier. This can have a major impact on the costs accrued by the company.
FEATURES AND CHARACTERISTICS OF THE SYSTEM
Installation of the system can be carried out extremely fast, due to a solution based on the „plug&play” principle through which it can be connected easily to any SMT production line. The newly developed SMEMA control box (Bi-Box) creates a link between the production line and physical reality. The Bi-Box integrates into the standard SMEMA communication channel existing between individual machines of the production line. Therefore, the type of any individual machine does not affect compatibility. The intervention units are equipped with high-performance, IoT capable microcontrollers. These microcontrollers can access the network through wired connection, which means they fulfill the basic requirements for Industry 4.0. The system does not require any regular maintenance, and it is reliable for long term use.
The system:
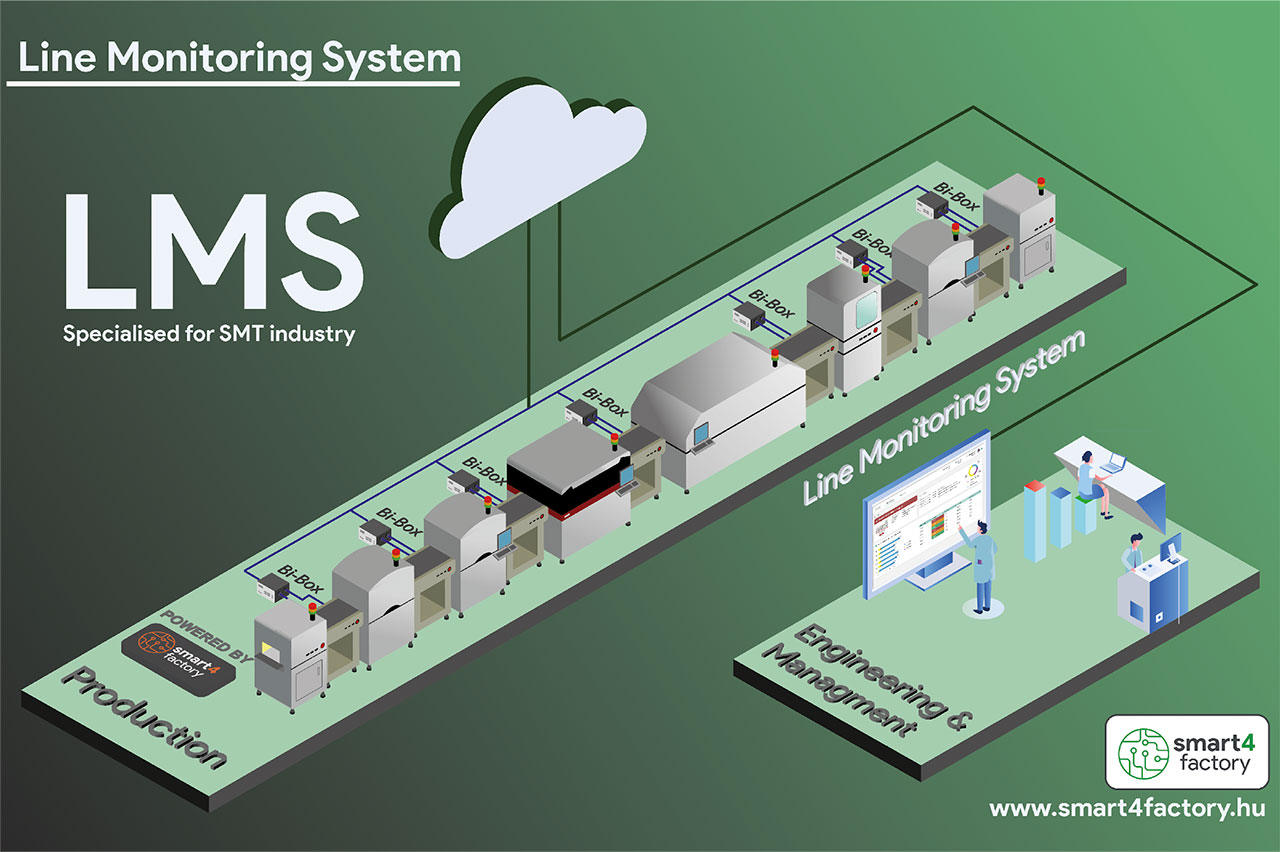
CONDITIONS NECESSARY FOR THE INTEGRATION
The system is designed to be installed easily and extremely fast. Therefore, the following four conditions are the only ones that need to be fulfilled:
- Server: connection to local or cloud-based servers.
- SMEMA Bi-Box: an interface developed by our company, which integrates into the communication between two devices. In order to operate, it requires a 12V voltage supply and connection to the network.
- Display: the monitoring system can be accessed via a browser and provides a live image.
- Wired or wireless network: connection between server and Bi-Box on RJ45 network.
ADVANTAGES PROVIDED BY THE SYSTEM
- Continuous monitoring of the production line: direct feedback facilitates faster reaction to any given defect or failure, thus enhancing efficiency and capacity.
Screenshot from the system:
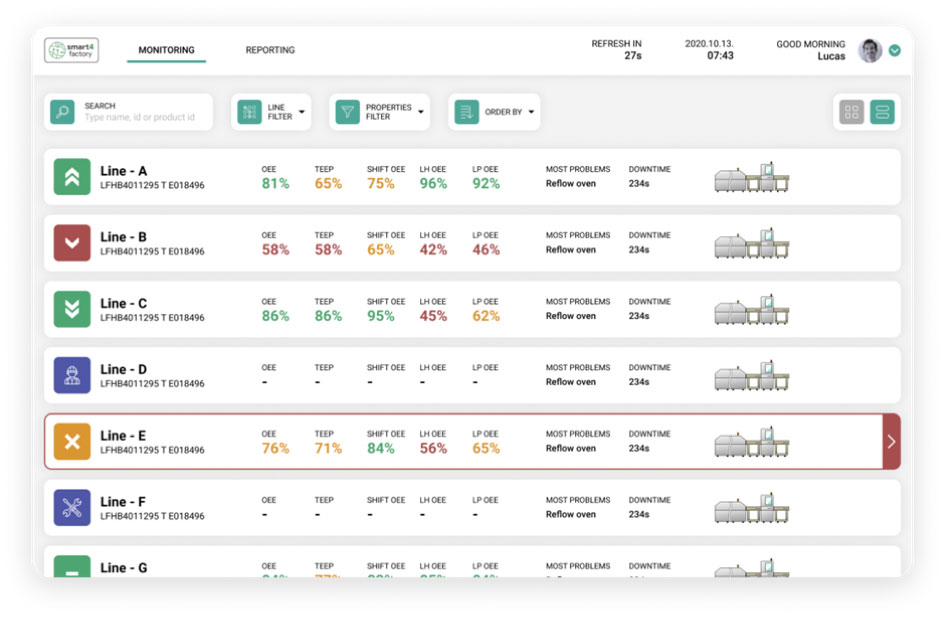
- Enhanced efficiency: faster response directly decreases individual downtime periods. Accurate data on downtime periods helps to optimize process design.
- Notifications, traceability: it can happen during production that one of the pick-and-place machines loses its cycle time, which will only be shown by a decrease in the number of pieces produced per hour.
- Strategy: Accurate data helps to make good strategic decisions and can be used to develop and implement a fair bonus system.
Contact details:
Adress: H–9021 Győr, Szent István út 10/A
Contact person: László Szabó, CCO, +36 30 905 7262, This email address is being protected from spambots. You need JavaScript enabled to view it.